County more than diamond in the rough
Innovation helps Zhecheng become numero uno in rapidly growing gem industry
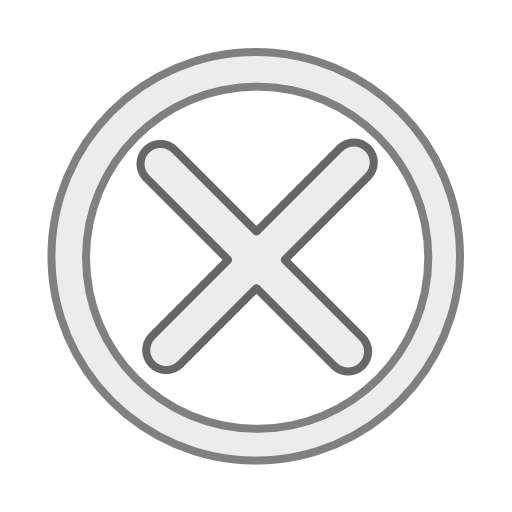
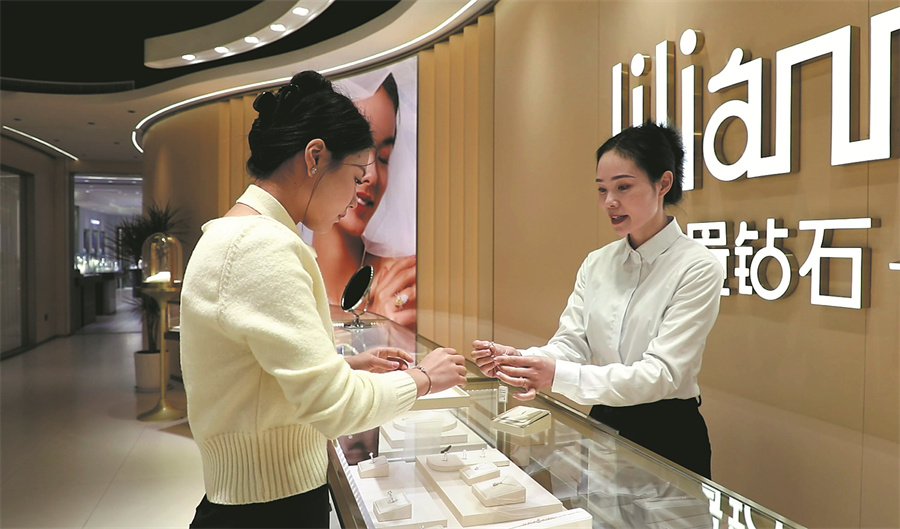
Four decades ago, Zhecheng, an agricultural county in Central China's Henan province, was mainly known for its chili peppers and beef cattle.
Today, by churning out an annual production of 6 billion carats of diamond single crystal, 15 billion carats of diamond micro-powder, and more than 10 million carats of lab-grown gems, the county now dazzles as the "diamond capital of China".
Synthetic diamonds, also known as lab-grown or man-made diamonds, are created in controlled laboratory conditions rather than formed naturally. The sector is mainly divided into consumer-grade diamonds and industrial diamonds that include diamond micropowder and single crystal.
In 2023, China produced over 70 percent of the world's synthetic diamonds, totaling 22 million carats, and Zhecheng was responsible for nearly half of that glittering output. Last year, its share further increased to about 60 percent.
How did a once modest farming county emerge as a powerhouse in the global superhard materials industry — once dominated by giants from the United States and Russia?
Sun Ruomei, Party secretary and director of the management committee of Zhecheng High-Tech Zone, said that the growth of Zhecheng's diamond industry doesn't represent "Rome built in a day".
"Years of unwavering support from pioneering enterprises, visionary policymaking from the county government, and a relentless drive for innovation and digitalization from the younger generation are the reasons," Sun said.
The story began in the 1960s, when China relied heavily on imported diamonds to drive industrial development. Determined to chart its own path, the country embarked on an ambitious quest to produce synthetic diamonds, with Henan emerging as a pivotal player in this high-stakes undertaking.
After years of trials and setbacks, China successfully created its first synthetic diamond in 1963, becoming the fifth country to achieve this technological feat after the US, the former Soviet Union, and others.
But Henan didn't stop there, and designed a groundbreaking six-sided top press that turned soft graphite into glittering diamonds with astonishing efficiency — 20 times faster than two-sided presses used abroad.
The presses not only accelerated production, but also laid the foundation for a revolution in the global superhard materials industry.
Yet these just represented the first step, and scaling up mass production became a game-changer. One of the first to seize the opportunity was Wang Zhanxi, a 70-year-old worker from Zhecheng. He founded the county's first diamond tool factory, aiming to not just produce diamonds, but also to churn them out at scale.
Wang said that technology thrives only with willing markets. Thus, in his early years of enterprise, he often braved frigid winters to promote diamond micropowder at trade fairs in Beijing to expand the market.
"Wherever there was diamond production, the Zhecheng people were there buying raw materials. Wherever there was a diamond fair, the Zhecheng people were there promoting micro-powder," he recalled.
Thanks to Wang and a determined team of Zhecheng entrepreneurs, the county has grown to become the mecca of China's burgeoning superhard materials industry, producing everything from industrial diamonds to lab-grown gems that dazzle in luxury jewelry store displays.
Today, Zhecheng boasts a 12-square-kilometer industrial cluster that links upstream suppliers with downstream manufacturers in the superhard materials industry. It has also created a seamless ecosystem that has drawn over 120 diamond-related enterprises, including two national-level little giant companies celebrated for their innovation and market dominance.
Among the two little giants companies is Huifeng Diamond. Once a humble family workshop, it has evolved into the nation's largest producer of diamond micro-powder, churning out an astonishing 3 billion carats annually.
At Huifeng's ultramodern factory, the hum of 300 sorting machines and 30 high-speed centrifuges has replaced the din of manual labor.
Workers are a rare sight, thanks to digitalization that governs every stage of the production process. From sourcing raw materials to shipping out finished products, every process is tracked in real time, ensuring precision and efficiency.
"This new equipment is a game-changer," said Bao Siwei, Huifeng's deputy general manager. "What used to require hours of manual work is now fully automated. Our efficiency and quality have skyrocketed."
Huifeng's crowning achievement is the industrial-scale production of 50-nanometer diamond micro-powder — a feat that places it firmly on the global stage. "It's this innovation that cements our position in the international market," Bao said.