Hongrun eyes bigger global market share
Specialized equipment maker steps up expansion with cutting-edge tech
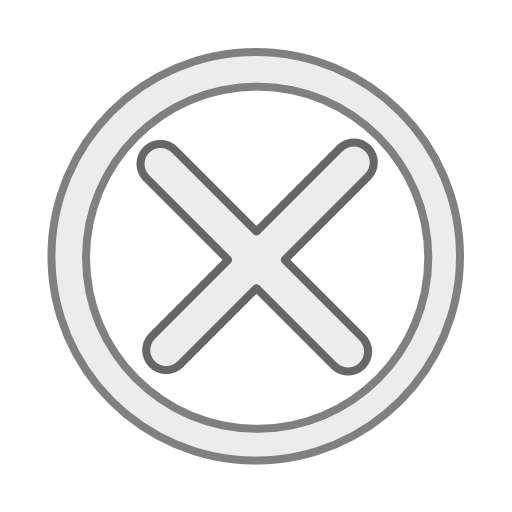
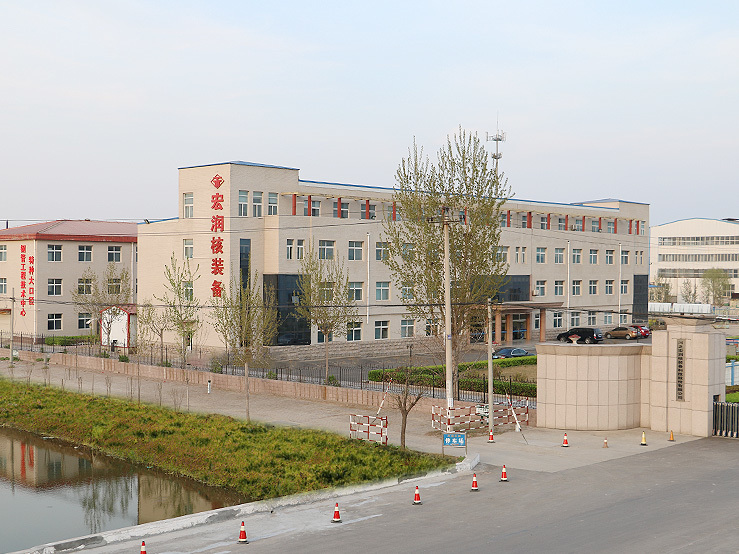
Eyeing tremendous opportunities abroad amid an accelerated transformation of the global energy landscape, Hebei Hongrun Nuclear Equipment Science and Technology Industry Co Ltd has vowed to step up its international expansion with the world's largest 50,000-metric ton vertical extrusion press.
After launching the machine 12 years ago at an investment of 500 million yuan ($69.04 million), Hongrun Nuclear Equipment saw its revenue from overseas climb, with its total export value in 2023 reaching 130 million yuan, accounting for 30 percent of the company's total revenue.
This share is expected to increase this year, it said.
Overseas orders have mostly come from fields including oil and gas, nuclear power, as well as hydrogen energy from Japan, the Middle East, Europe and the United States, said Liu Chunhai, chairman of Hongrun Nuclear Equipment.
Orders to well-known international companies accounted for over 40 percent of the export share, including a water-cooled equipment worth $9 million for Japanese steelmaker NKK Corp, a $20 million pipeline project for a US boiler company, and a $15 million pipeline project for a power plant in the United Arab Emirates, Liu said.
The machine is still currently the largest of its kind globally, breaking significant technical barriers in the production of large-diameter, thick-walled pipelines and has redefined traditional forging design concepts, achieving crucial technological advances, said the company.
This advanced extrusion machine can produce seamless steel pipes up to 1.32 meters in diameter and 13 meters in length. Designed to handle high-strength materials, it serves essential sectors such as nuclear, aerospace, and defense.
"Through more than a decade of continuous investment in equipment, the quality of domestically produced steel pipes has steadily improved, allowing us to reach new levels of quality and efficiency," said Liu.
China, despite being the world's largest steel producer by volume, has long struggled with specialized high-grade materials and had to remain dependent on imports. One of the roots of this problem remains the extrusion machine.
After decades of research and development, China finally unveiled its own 50,000-ton hot extrusion machine in July 2020, which is capable of producing high-grade steel pipes at a cost far below those of imported alternatives, with the material utilization rate increasing from 50 percent to over 70 percent.
An analyst said China is now poised to become a major exporter of high-grade steel pipes and possibly the extrusion machines themselves as continuous technological breakthroughs could reshape global supply chains and trade relationships, particularly in industries such as oil and gas, aerospace and defense.
"This technological cross-pollination could lead to advancements in fields ranging from construction to space exploration, further amplifying the impact of China's achievement," said Lin Boqiang, head of the China Institute for Studies in Energy Policy at Xiamen University.
A key breakthrough of the machine is its role in manufacturing G115 and P92 steel pipes, which are essential for ultra-supercritical power units.
The domestically developed G115 steel was recently applied in the Datang Yuncheng 630 C ultra-supercritical reheat project, raising turbine inlet temperatures to 631 C. This project overcame a 620 C bottleneck, pushing coal-fired power generation efficiency above 50 percent for the first time.
The G115 high-temperature steel, jointly developed by China Baowu Steel Group and Hongrun Nuclear Equipment, is China's first domestically developed power station steel with complete intellectual property rights.
Chen Jiasheng, a senior vice-chairman of the China Energy Research Society, said the widespread application of G115 will drive the clean and efficient use of coal-fired power, which is crucial for balancing energy demands with environmental goals, especially in countries with significant coal reserves like China.
Chen said improving the efficiency of coal-fired power plants, such as through ultra-supercritical technology, allows for more energy to be generated per unit of coal, reducing both fuel costs and emissions.