Weaving a brighter future for traditional craft
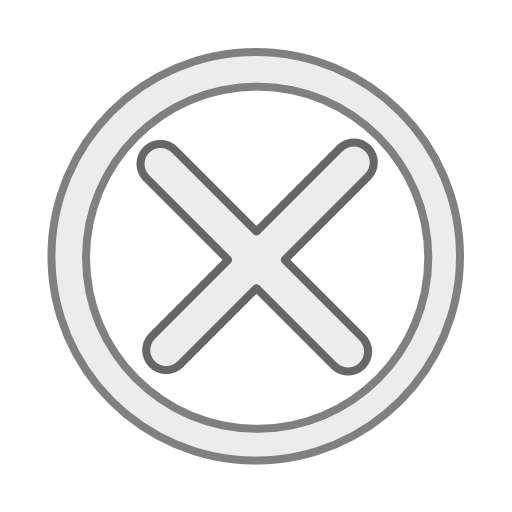
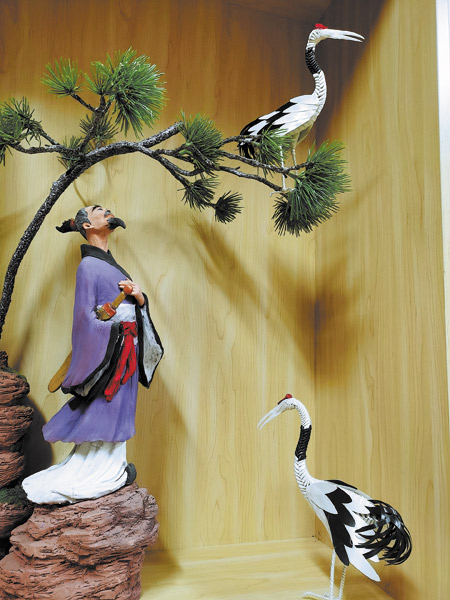
To complete a work, Wu says she is meticulous about planning, production and revision, a practice the young woman adheres to with every piece.
Different pieces need different materials, Wu says, adding that products modeled after insects are usually made using leaves from palm trees or reeds, while hats, small baskets, and big animals are mostly made using straw.
Wu explains the process of straw weaving: "When the wheat is ripe, pick the top part of the straw, the one with the ears of wheat, as it is longer. Then tie them up and dry them. Before knitting, the wheat straws need to be soaked in warm water to make them more flexible and avoid them breaking."
A layman might think that the work is just about the actual weaving. According to Wu, however, selection of materials is the first step of a complicated, time-consuming and labor-intensive process that can take weeks, or even months, to complete.
"You need to sketch the piece on paper, which requires drawing skills, and also conceive its three-dimensional structure. Next comes the weaving, shaping and finally the preserving of the work," Wu adds.
"Even by adhering to that process, it does not mean that you will always create a good piece of work, and the hardest part is to make it lifelike and solid," Wu says, adding that, to this end, she will take pieces apart and try again.
Wu recalls that, when she was a child, woven straw items could be found almost in every household in the countryside, such as straw hats and straw shoes, because they were practical in everyday life.
"Due to the impact of industrialization, manufactured goods have replaced such products, which yield low profits, and there are only about 100 individuals engaging in the work across the country," she notes.
"The world has changed, and craftsmen need to transcend practicality and pursue the beauty and artistry of straw culture to help the craft survive and thrive," she says.
